|
|
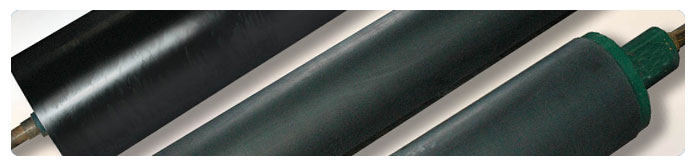 |
 |
|
Böttcher varnishing roller coverings have been developed with an eye on the special requirements of varnishing units in printing presses. They are characterised by a particularly homogeneous surface, good dimensional stability and optimal ink and fountain solution transport. To ensure that Böttcher varnishing roller coverings obtain best possible results and reach a long service life, the following Operating Instructions should be observed: |
|
|
Transportation and Storage |
|
Varnishing roller coverings must not have any contact with load suspension devices during transportation and have to be protected against the impact of direct blows. When lifted with lateral lifting slings, squared timbers have to be used for the protection of the front sides. Rollers may only be stored on their journal, not on the surface of the covering. The covering has to be protected against direct action of light and heat. Storage in a cold environment has to be avoided as well. The original wrapping paper supplied by Böttcher warrants the necessary protection from light and should be left on the roller covering, to be removed just immediately before use. |
|
|
Roller Pressure and Printing Strip Width |
|
A roller will only achieve its desired function permanently, when adjusted correctly. In general, the following has to be observed for the application of cleaning and care products:
Materials, which are resistant against oleo-resinous varnishes, and water varnishes (e. g. 496 80, 494 70) may well, when exposed to UV-varnishes, destroy the roller coverings in most cases. |
|
|
Cleaning |
|
To ensure a long service life and precise printing, the rollers have to be cleaned with a suitable cleaning and care product after every printing job, prior to ink changes and, in case of high print volumes, also in between. Furthermore, the rollers have to be thoroughly cleaned, inspected and regenerated with suitable care products at intervals not exceeding 4 weeks, or, when subjected to special strains - such as fast-drying inks or linting papers - at considerably shorter intervals. For cleaning and care of Böttcher printing roller coverings, Böttcher with their brand Böttcherin offer a range of special cleaning and care products, which are tuned to Insufficient impression pressures will - due to tolerances in concentric running and cylindricity -lead to uneven varnish transport. Excessive impression pressures have - due to internal friction and pressure overload - a negative effect on the life of the roller covering.
To avoid an uneven impression pressure and the resulting pressure overload, it has to be ensured, that the roller is always adjusted parallel to the counter roller. When adjusted in parallel, a printing strip of even width is obtained over the entire length of the contact area. During pro-longed rest periods, the roller covering has to be released from load by throwing off the roller, to avoid permanent deformation. |
|
|
Chemical Resistance |
|
Roller coverings are exposed to stress by chemical substances in the operating media, such as varnishes and fountain solutions as well as cleaning agents and care products. Böttcher offer roller covering materials, which are specifically tuned to different printing processes and operating media. Special operating media, such as fast-drying inks, UV-drying inks or special varnishes may require the application of roller coverings of a specific material. Such special cases and any problems arising with the cleaning agents and care products used require consultation by specialists from Böttcher. different operating media and roller materials. The use of Böttcher cleaning and care products warrants - apart from good cleaning action - maintenance of the roller covering.
For materials suitable for oleo-resinous and water varnishes (e.g. 496 80, 494 70), contact with UV cleaning agents should be avoided, because this may lead to swelling.
Tools with sharp edges, such as steel brushes or emery paper must not be used for cleaning under any circumstances. |
|
|
Levelling and Re-Grinding |
|
After longer operating times, due to the impact of operating media and other influences, hardening and glazing of the roller surface may occur, which cannot be eliminated with cleaning and care products any more. Hardening of the roller surface is also indicated by an increase in the Shore hardness measured on the surface. In such an event, the functionality of the surface finish can be restored by levelling, i. e. light re-grinding of the roller covering. |
|
|
|