|
|
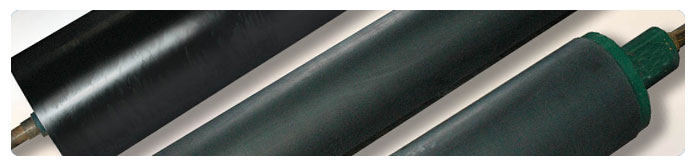 |
 |
|
|
Fluoroplastic Sleeves |
Path Rollers |
Web guide or path rollers are an important and often critical component of every newspaper press. They have a direct impact on print quality and require a considerable amount of cleaning and maintenance time, very often in positions that are difficult to access. Deposits of ink and paper residue on the path roller lead not only to soiling of the print product itself but also to register problems and creasing.
As the world’s leading producer of elastomer-covered rollers for the newspaper printing industry, Böttcher has carried out extensive research on these problems and invested substantially in the development of new types of surface coatings and processing methods. These anti-adhesive surface coatings minimize ink set-off, make the removal of ink deposits much easier and extend cleaning intervals. In light of the increasing use of colour and the substitution of spot colours in 4C newspaper printing – which inevitably results in higher ink coverage – Böttcher path roller coatings can make a significant contribution to cost-reduction and the improvement of print quality.
Fluoroplastic Sleeves
Böttcher InkStop fluoride-plastic shrink sleeves are designed for use as coatings for path rollers. By virtue of their specific surface chemistry, these sleeves have very strong anti- adhesive properties and thus inhibit the formation of ink deposits.
Because InkStop sleeves are highly resistant to aggressive media, exposure to printing inks and chemicals commonly used in the printing industry poses no significant problems. Due to their excellent temperature resistance, InkStop sleeves can be used in environments with operating temperatures up to 200°C. Even when exposed to high physical stress, the sleeve retains sufficient strength at temperatures as high as 100 – 120°C. The sleeves have a uniform light-blue surface, which facilitates the recognition of initial ink build-up. |
|
Application |
The appropriate InkStop sleeve is selected for the specific diameter and length of the guide roller to be coated, allowing for slight overmeasure in all directions. The sleeve is then pulled over the roller and shrunk to fit the roller core with a hot-air blower. Shrink-fitting can be performed by our sales and service centres or at the user's printing facility.
For users who wish to shrink-fit sleeves themselves, Böttcher offers a specially designed shrink-fitting unit that facilitates handling and minimizes the risk of creasing and bubble formation. This enables customers to eliminate the transport operations and waiting times required for off-premises coating without sacrificing quality. |
|
Cleaning |
Path rollers with a InkStop surface can be cleaned using a cloth and a wash. It is not necessary to use mechanically abrasive cleaning agents or sharp instruments, which may cause damage to the InkStop surface. |
|
Important information |
Experience has shown that plastic sheeting and sleeves may accumulate electrostatic charges under certain operating conditions. This can cause electrical discharges from the surface of the sleeve. In order to reduce the risks associated with electrostatic charges (risk of shock and / or ignition), we recommend the use of water-based washes, such as Böttcherin Turbo for cleaning the path roller surface. Further, volatile, highly flammable liquids (flash point <21°C) should not be used in the area of potentially electrostatic charged sleeves.
As a preventative measure, electrostatic charges in coated rollers can also be discharged manually using tools designed for this purpose. In any case, sufficiently high atmospheric humidity in the pressroom and grounding of the roller cores are essential.
The sleeve must not be exposed to temperatures above 270°C during the fitting process. At temperatures above 270°C, the sleeve material may disintegrate, resulting in irreparable damage to the coating. |
|
Advantages at a Glance |
 |
Anti-adhesive surface guarantees minimum set-off. |
 |
Reduced cleaning time required to remove ink deposits, resulting in fewer working hours, labour costs, solvent consumption and emissions. |
 |
Longer cleaning intervals, leading to further reductions in working hours and labour costs. |
 |
Ink smears on print products are avoided, resulting in improved print quality. |
 |
Lower risk of creasing and register problems contributes to an optimum printing process. |
 |
Initial ink build-up is easily recognizable on the light-blue roller surface. |
 |
Guide rollers are cleaned on an as-needed basis, makes maintenance planning easier. |
|
|
This newly developed product is another addition to the extensive program of products and services for the newspaper industry offered by the Böttcher Group. In addition to inking, damping and paster rollers, Böttcher also supplies printing chemicals developed specifically for newspaper production and offset printing blankets for all press configurations. |
|
|
|