|
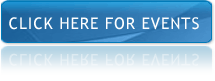 |
News |
|
|
Innovative Roller Coverings for Film Dampening Rollers |
The advent of film dampening systems in offset printing represented a huge leap forwards in terms of print quality and productivity. Printers could now react more quickly than before to control the printing process and it was much easier to maintain a stable ink-water-balance, even at high press speeds. In film dampening systems, the dampening film is formed by the dosing and spreading activity of the rollers. The specific positioning of each roller in the dampening train, combined with the properties of the roller coverings in the individual positions, are the main factors in determining the quality and consistency of the dampening film and - with that - print quality. The formation of an even film can also be supported by the addition of IPA to the fountain solution.
A new awareness and legislative situation with regard to health and safety and environmental issues, along with significant and increasingly incalculable variations in the price of IPA have in recent years encouraged press operators to reduce or even eliminate the use of IPA in offset printing.
Higher press speeds, reduced levels of IPA and - last but not least - new developments in the chemistry of offset inks place new and very particular demands on both fountain solution additives and dampening rollers in modern offset presses. When selecting the ideal fount additive and roller materials for a given application, consideration has to be given to the specific demands of each press configuration and the inks used. Finally, the quality and economic expectations of the customers and the operating conditions of the individual printing company have to be taken into account.
Böttcher has developed a broad range of dampening roller compounds to cater for all these parameters, as in today's complex global environment, the key to success is not one single concept, but the intelligent combination of the many different options to suit the individual customer's situation.
|
|
The Influence of Dampening Rollers in Offset Printing |
Each roller position in the dampening train has a very specific and unique role to play in the printing process. Particularly in modern presses and with reduced or no use of IPA, this calls for customised covering materials for each roller position. |
|
Demands on Dampening Rollers |
The form dampening roller takes the fountain solution from the transfer roller and applies it to the printing plate, at the same time ensuring the correct degree of ink-water-emulsification.
When the film is transferred to the form dampener, the fount film is stretched, since the form roller rotates at a significantly higher speed than the hard pan or metering roller. It is important that a certain amount of water is integrated into the ink, as it is largely this integrated water which ensures that fine negative lines in the printed images are kept open as this water is released again when the film is applied to the printing plate. Specialised form roller compounds can actively support this process. |
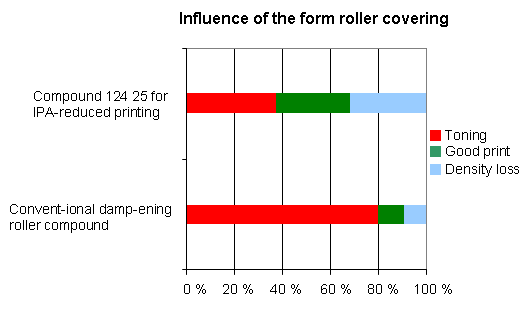
Damp settings |
Damp Settings shows the influence of the form dampening roller on plate wetting. It compares a conventional dampening roller compound with a form roller compound for IPA reduction (124 25). Under the same conditions, the optimised compound wets the plate at significantly reduced water settings. At the same time, the operating window between toning and loss of density due to plate flooding is also much larger.
Form dampening rollers are in continual contact with ink and ink-water emulsions, and must therefore be chemically resistant to the inks in use. An inking roller compound would obviously also afford this resistance, but would provide inadequate dampening performance.
Böttcher has been supplying the 124 25 compound for alcohol-reduced or alcohol-free printing in conjunction with conventional offset inks for many years and with great success. For UV and dual purpose printing, the new compound 134 25 has been added to the Chameleon series of compounds. This compound offers both excellent dampening properties and extremely high dimensional stability in both UV and conventional inks. |
|
Demands on Pan and Metering Rollers |
The primary job of pan and metering rollers is to provide a consistent dampening film. The hard pan or metering rollers have to accept the water film in the nip and subsequently transfer it evenly to the form dampening roller. Inconsistencies in this film have an immediate negative effect on the printed image. |
|
Negative Physical Phenomenae During Film Splitting |
Dynamic disturbances in the flow of the liquid in the transfer nip can lead to printing problems. For example, the phenomena of cording, which can arise in the separation phase of the nip between the pan and the metering roller, can be carried forward to the printing plate and be visible as fine lines in the printed image. Stripes of this nature are a result of dynamic film-splitting processes, their occurrence depends on a number of factors, such as the rotational speed of the dampening rollers, roller settings, temperature, the viscosity and surface tension of the fountain solution and many other parameters.
Even small variations in any of these parameters can give rise to or prevent the occurence of these stripes. With regard to the pan roller, the problem can be approached from different angles, depending on the specific situation on a given printing press.
For many printers with mid- or large-format presses - particularly in packaging applications - the problem could be solved by the use of pan rollers with a rougher, but clearly defined surface structure, which significantly increased the ability of the roller to mechanically pick up and carry a higher volume of water. This in turn allowed the operator to reduce the speed of the roller in the dampening train, thereby removing the potential for cord stripes to arise. In other cases, the use of a different rubber compound which retained a higher degree of elasticity at low temperatures had a positive influence on the film splitting process and eliminated the appearance of cording.
The new ProAqualis generation of pan roller coverings its special surface technology gives the printer unparalleled performance in splitting and transferring an even film of dampening solution. |
|
Negative Chemical Reactions and Side-Effects |
During the printing process, a disturbance of the ink-water-balance can lead to ink feeding back onto the dampening pan roller, which leads to a number of problems. Often, the ink feedback occurs in localised, radial structures, as is shown in Fig Ink feedback onto the dampening pan roller (left).
Depending on the type of ink, the covering material on the pan roller and the fount additive in use, this feedback can quickly lead to localised radial swell of the pan roller covering and to a variety of print problems.
|
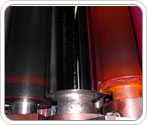
Ink feedback onto the dampening pan roller (left) |
|
So far, it has not been possible to fully identify all factors contributing to this problem, but it has been possible to replicate the problem in a specially adapted dampening unit simulator. This in turn enables the researcher to identify the scale of the potential problem when using different roller covering materials, while at the same time investigating the influence of different fount additives and other materials and parameters in the occurrence of the problem.
Based on the results of this research, the classic dampening roller compounds have been further developed and refined, leading to the introduction of the compound 147 25 as the standard compound for both dampening pan and metering rollers with the highest level of protection against radial swelling.
However, in practice, there still remain some combinations of ink and fount additive which - in extreme circumstances - can cause a degree of residual radial swelling, even on this compound. |
|
The Solution: The New Pan Roller Compound ProAqualis |
The use of a composite roller covering represents a new, innovative alternative to homogenous rubber coverings. Such a composite solution is the ProAqualis covering, which consists of a customised dampening roller base compound to which an additional functional coating is applied. This coating is made of a highly specialised elastomer material, which is chemically extremely resistant to the components of both inks and fount additives and protects the base rubber layer from attack by these materials. The coating process results in a matt surface of defined roughness, combining excellent water transfer capability with ink-repellent properties and virtually complete insusceptibility to swelling. The highly dynamic base rubber guarantees the necessary elasticity and adaptability in the roller nip for optimum performance at all press speeds.
A specific advantage of the ProAqualis system is its high degree of compatibility with roller washes and the polar solvents typically contained in many dampening and metering rollers cleaners and uv washes available in the marketplace.
The ProAqualis rollers have been successfully tried and tested in a large number of both sheet-fed and web presses, typically running at IPA levels of between zero and 8%.
ProAqualis has also become the standard pan roller covering on new presses for several of the leading press manufacturers. |
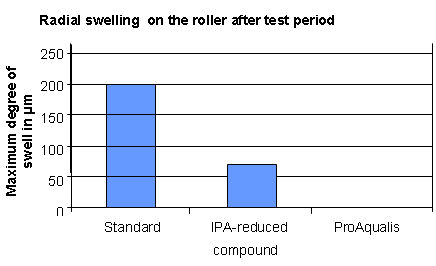
Level of radial swell on different rubber compounds |
|
Fig. (Level of radial swell on different rubber compounds) shows the results of a test series in which 3 different dampening roller compounds were exposed for a defined period of time to swell-inducing materials. After exposure, the degree of swell was determined by measuring the rollers on a laser measuring device Fig. (Laser measuring device.) |
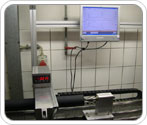
Laser measuring device |
|
|
The Böttcher Roller System for Dampening Units: ProAqualis |
The new, extremely swell-resistant covering for pan and metering rollers ProAqualis 128 25 and the 124 25 compound for form dampening rollers in conventional offset applications and the Chameleon compound 134 25 for UV and dual purpose printing are innovative solutions for offset printers. |
|
Events |
|
Third Annual Sales Meet " 4th Oct. 7th 2010" GOA
Boettcher India had 3rd annual sales conference at serene and splendid environment of "Goa" surrounded by beautiful Beaches at hotel "o" from 4th to 7th Oct. 2010
Mr. Bhaskar Joshi, Sales Controller had the inaugural address of the meet followed by presentation sales people from different zone.
Country manager Mr. N.C. Jha also dwelt upon the Planning & Strategy for achieving an ambitious target of INR 100cr. Turn over in the next financial 2011.
Conference also witnessed the brief introduction of various" New Product" in different Product segment, which is reflective of our commitment to Printing world for better Printing
RUBBER ROLLER
Pro Aqualis - Roller is going to be introduced with upgraded rubber compound
Golden Pearl - Hard Thermoses Roller
CHEMISTRY
WASH -
New Eco & Human friendly with high F.P.> 65 deg wash with Improved cleaning Power
Boettcher Mistral & Twister
NEW FOUNTAIN -
Heat Set Fount- H 2010
Cold Set Fount - N1004 GA
BLANKET
BT-7400 - Multi purpose Blanket 4 ply
Sales person were also made abreast of recent development & fast changing scenario of printing Industry, also had the free exchange of idea between sales people for the future growth.
|
Analyzing the Fountain behaviour |
|
|
|
|
|
Brainstorming session |
|
|
|
|
|
|
|
Future Planning |
|
|
|
|
|
Maitaining the old tradition with new development |
|
|
|
Understanding the customer wave of query |
|
|